
FREQUENTLY ASKED QUESTIONS
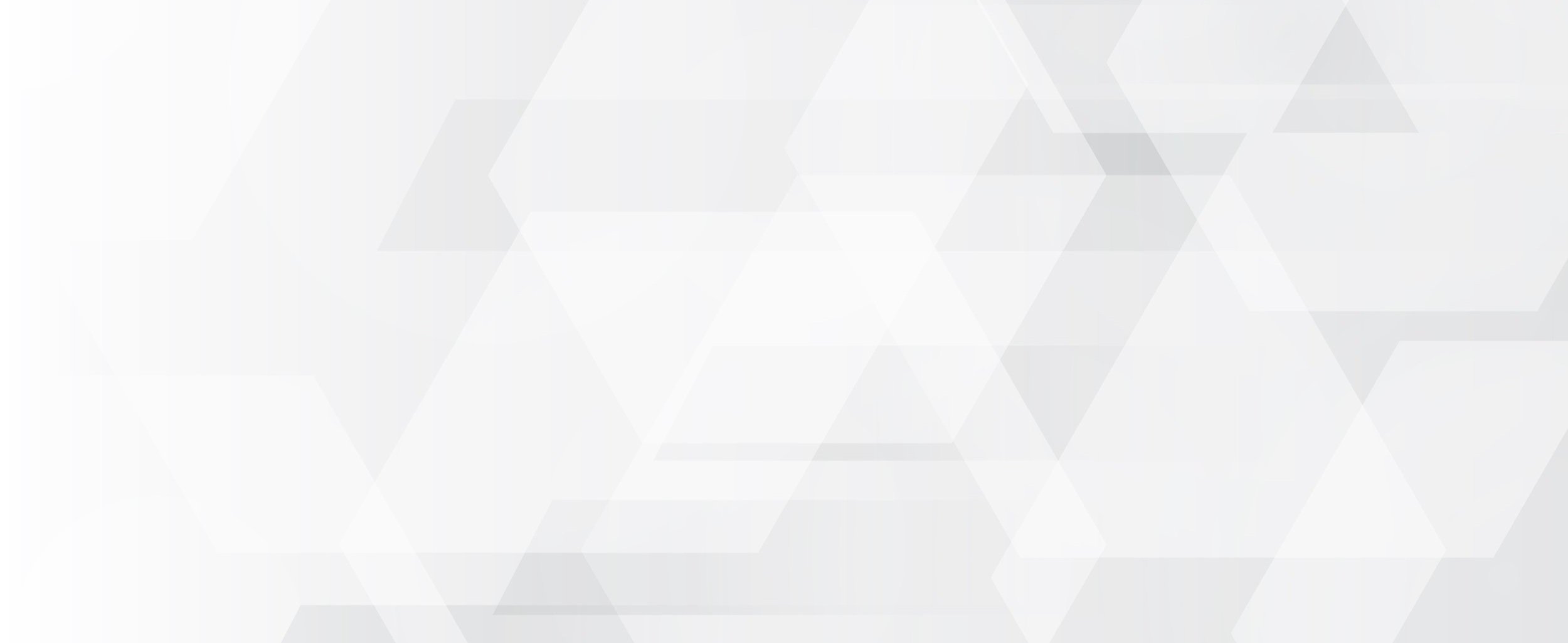
-
LX Construction exists to acquire and operate 3D concrete construction printers and associated robotic technology, which will provide substantial innovation to America’s largest industry.
-
Our research indicates that the lowest risk opportunity to leverage this technology is as an operator rather than the developer/creator. Understanding this, we undertook an extensive investigation process to determine which 3D concrete printer manufacturer is leading the industry, and we selected a company out of Denmark called Cobod. Here is a brief video of the specific printer LX will be acquiring: Bod2 Printer Video.
-
The cost advantage mainly comes from the lower labor usage, the faster project completion, the assurance of fewer mistakes, and the need for less coordination, as the printer and its associated software take care of many operations. The speed at which you can print and execute a project will depend on your previous experience. Hence, you will be much faster once you have done it a few times.
The key advantage of using this technology includes a 20-25% reduction in overall construction costs and a 50% reduction in total construction time. In addition, there is substantially increased design flexibility and limited locally sourced supply inputs. It is well known that there is a current national housing shortage and affordable housing crisis exacerbated by supply chain constraints resulting in substantially increased construction costs. Without innovation, it is evident that this industry will either come to a standstill or cause continued increased housing prices.
-
The printed homes are expected to last as long or longer than standard Concrete Masonry Unit (CMU) built homes, which is 100+ years according to the International Association of Certified Home Inspectors (InterNACHI). The houses are made according to the International Building Code (IBC) structural code standard.
-
The process will vary from project to project, but a standard building will consist of:
-Site preparations
-Printer installation
-Printing outline of slab/foundation
-Casting slab/foundation
-Printing walls for ground floor
-Installing deck
-Repeat for multi-story buildings
-Closing the house (roof, windows, doors)
-Finishing (paint, floors, electricity, HVAC) -
The ICC – Evaluation Service (ICC-ES) has created a document known as AC509 which provides the support that local municipalities require that the construction methods for 3D printed walls conform to existing building standards.
Recently, the AC509 was revised to include multi-story buildings and fire ratings.
Concrete as a material is currently being used in construction methods, so ultimately the variation we are requesting is to simply change the application method.
-
Conventional construction is slow, fragmented, wasteful, and has poor thermal properties which increase energy use, increase operating costs, and decrease comfort. Also, conventional materials like drywall and particle board are some of the least resilient materials ever invented.
By contrast, 3D printing offers the following:-Speed
-Decrease in manual labor
-Concrete is a well understood, affordable, resilient material
-Concrete has a high thermal mass (comfort & energy efficiency)
-3D printing produces a continuous, unbroken thermal envelope (comfort & energy efficiency)
-Replaces multiple systems of the home in one technology (foundation, structure, insulation, interior & exterior sheathing, moisture barrier, finished surfaces, etc.)
-Near zero waste
-Tremendous design freedom (curves and slopes are no more challenging or expensive than straight, plumb lines). -
-The manufacturer of the printer has agreed to allow LX to send our printer operators to Denmark for four weeks of hands-on training which COBOD includes in the purchase price of the printer.
-LX has pre-identified individuals with unique experience operating similar machinery and as a subcontractor in the home building process.
-
Each COBOD BOD2 printer has cost just over $1M.
-
Turns out that both Lennar and D.R. Horton (the two largest home builders in the US) both have already invested in the technology. However, they did it as a passive investor into the start-up ICON. Ironically, the biggest players didn’t actually buy a printer; instead they are equity investors. ICON raised $200M in their series B round.
The large homebuilders are actually our exit strategy. We believe between 5-7 years from now that we will have substantially scaled and will be an obvious acquisition target for the homebuilders looking to skip the education curve of the technology.
-
Our research indicates that the unions are not actively involved in the homebuilding industry, and it is for this reason we have targeted this subset of the construction industry first.
-
Our due diligence lead Lilly Capital to believe that the best way we could serve our investors would be to create LX Construction and acquire multiple printers to achieve substantial scale in the Midwest. First to the Midwest market and first to scale.
-
As an addition to the construction industry, we found it beneficial to utilize the winter months to run the printer(s) as manufacturing tools to produce items previously created as precast concrete. This manufacturing activity will be shown as septic tanks (offering 2) in the proforma. We believe quite a few products could be produced faster and cheaper than precast methods, such as septic tanks, fountains, benches, roadway barricades, etc.
Ready to ditch the limitations of traditional construction methods?